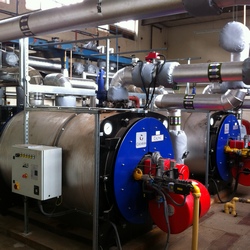
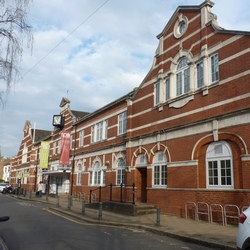
Leisure Project
Wimbledon Leisure Centre
- Location:
- Wimbledon, London
- Client:
- Greenwich Leisure Limited
- Cost:
- £500,000
History
Wimbledon Leisure Centre is operated by GLL for Merton Council. The Leisure Centre originally opened in 1901 and has a long history of providing recreation facilities for the neighbourhood. The centre still has many of its original features, making it a unique setting for the users. During the last few years over £1 million has been spent refurbishing the centre, which has made Wimbledon into Merton's premier leisure centre. The former sports hall has become a well-equipped gym, and facilities include a 30 m main pool, teaching pool, fitness studio, and crèche.
Project
EngDesign were commissioned by GLL to refurbish the plant within the centre. Many systems were redundant or in urgent need of replacement. The centre had to remain in operation, with minimum shutdown. A two-stage tendering process was adopted, allowing contractor input into the process. Overnight works prevented closure of the centre.
Heating
Redundant heating plant, equipment and pipework were stripped out. Two of the boilers were relatively new, each rated at 1.2 MW with 100% redundancy, and could be retained. New plate heat exchangers connecting to the existing systems, new pumps, valves, pipeline-mounted strainers, and dirt separators were provided, together with a new domestic hot water buffer vessel and plant. Pumps with variable speed drives were installed for energy savings. A new BMS monitors and controls the plant for maximum efficiency.
Venitlation
The ventilation systems throughout the centre were in poor condition. The Main Pool hall supply installation used a very old centrifugal fan, purpose-built into the basement and over 50 years old. Eoof-mounted extract fans were inoperative. The unit serving the Teaching Pool was the only plant in good condition and which could be retained.
A new Main Pool air-handling unit was installed. Positioning a combined unit in one space allowed heat recovery technology to be used, reducing running costs and increasing plant efficiency. The new plant now gives the optimum ventilation, avoiding condensation problems and saving energy.